Professors Christos Athanasiou and Adam Steinberg bring an experimental mechanics competition to the classroom.
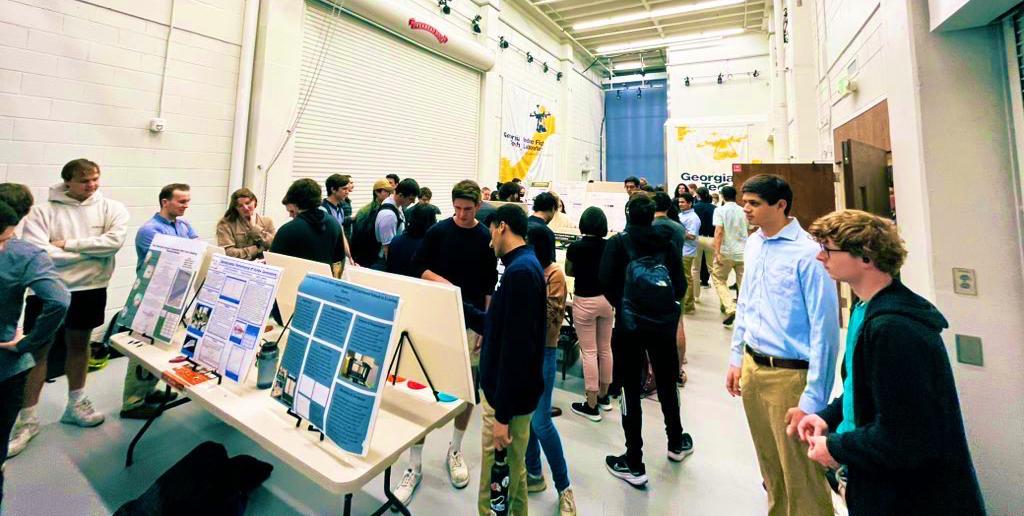
Students presenting in the AE 3610 competition in the Indoor Flight Lab.
The Experiments in Solid and Fluid Mechanics course offers students an immersive experience in the fundamentals of mechanics, guiding them through the design, execution, analysis, and presentation of cutting-edge experiments in both solid and fluid mechanics. This year, they added an exciting competition element to further inspire students to absorb as much mechanics knowledge as possible and refine their hands-on experimental abilities to the fullest.
The 36 teams were selected to work either on a fluid mechanics or solid mechanics-based problem of their choice, designing experiments, finding the resources to create test specimens, identifying the mechanical testing configurations needed, and finally analyzing results in a meaningful way.
Each team was given a budget of $100 to develop their assignment and two months to prepare and present their research to an open-house poster session before judges, professors Christos Athanasiou and Adam Steinberg, and eight teaching assistants. Students had to overcome logistical, financial, and material hurdles while developing their projects
“Working on the final project helps students develop 'street-fighting' skills – the kind that extends beyond traditional lectures, textbook problems, and theoretical knowledge."
Christos Athanasiou
Four on the Floor
Travelers don’t always think about flooring while boarding a plane and looking for their seats because they expect the floor to be sturdy and supportive. A team of plucky students decided to investigate the sandwich composite structure for airplane flooring using digital image correlation (DIC) with their project, Investigation of Core Configuration on Bending Strength in Sandwiched Composites. The winning solids team included Flavius Penescu, Marshall Williams, Aiden Wilson, and Ben Zabriskie, all fourth-year undergraduates.
“Many teams wanted to do fluids, so we chose solids. We wanted to be competitive in the process and differentiate ourselves, so we decided to use DIC. DIC is an image-based method allowing to measure strains and deformation, which is necessary for the design of more reliable aircraft,” said Williams, who plans to go into consulting after he graduates in the spring.
The team created a sandwich composite for airplane flooring using two steel sheets and foam. They attached two thin and stiff sheets to a lightweight, thick foam core. The material the team chose would be ideal for something like cargo plane flooring or wing materials. Therefore, this experiment explored how different core configurations of that middle piece in between the two steel plates affected the sandwich material bending stiffness relative to its weight. They measured it by the ratio of the bending stiffness of the material to its weight.
They analyzed the data from the DIC setup, which essentially tracks the movement of surface features during the experiment. This data, upon ‘special’ processing provides the strain maps that are developed in the sandwich material upon the application of an external force. From the experimentally obtained strain maps, they calculated the flexural stiffness and, eventually, the stiffness-to-weight ratios of each specimen.
“We experimented with drilling holes or cutting out certain patterns because, in theory, that would remove weight. Since the steel sheets weigh more than the foam, cutting out those holes made no significant decrease in the weight and significantly decreased the bending stiffness. So, we found that the solid flooring piece was the most effective,” Williams said.
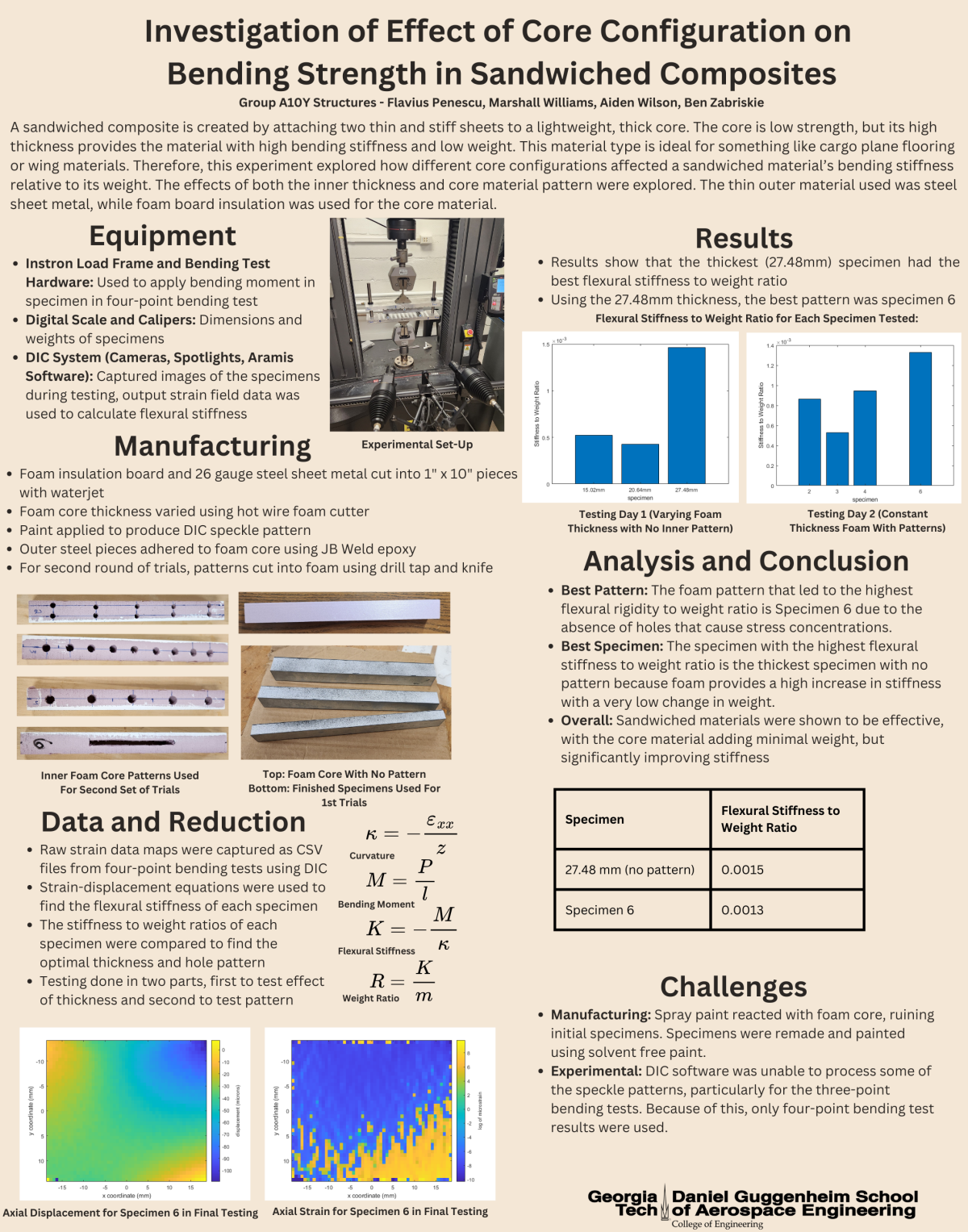
Investigation of Core Configuration on Bending Strength in Sandwiched Composites Poster
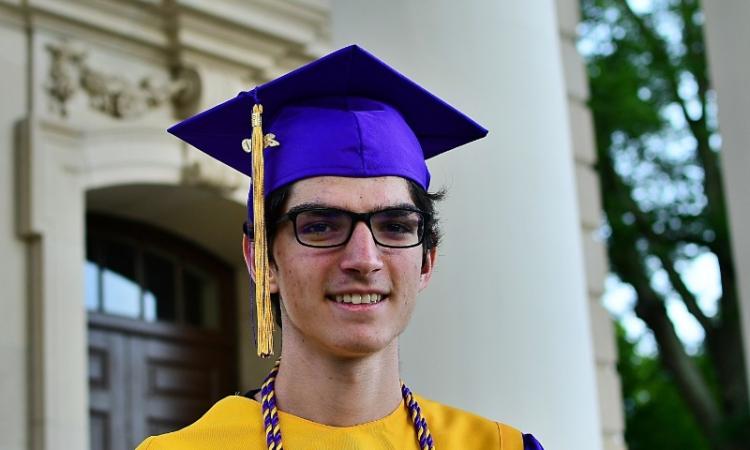
Flavius Penescu
Penescu, who hails from Atlanta, Georgia, was in charge of figuring out the best patterns and overall specimens and comparing them. He plans on pursuing his master's at Georgia Tech.
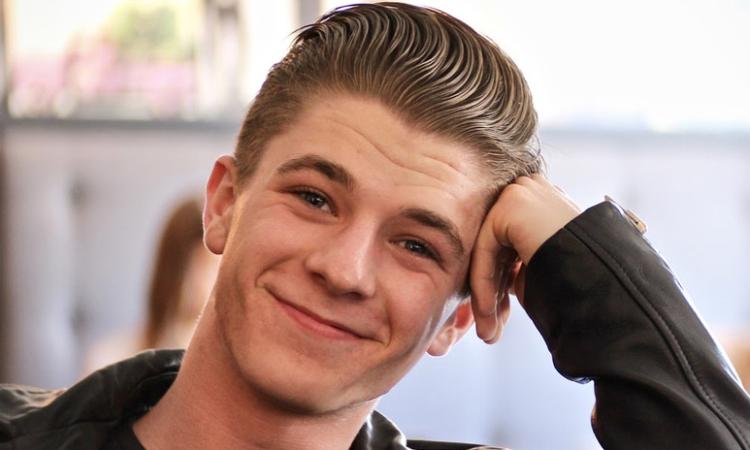
Marshall Williams
Williams was over the report because he did an internship at SCALE where he received a lot of experience in technical writing. He plans to go into management consulting after he graduates in the Spring.
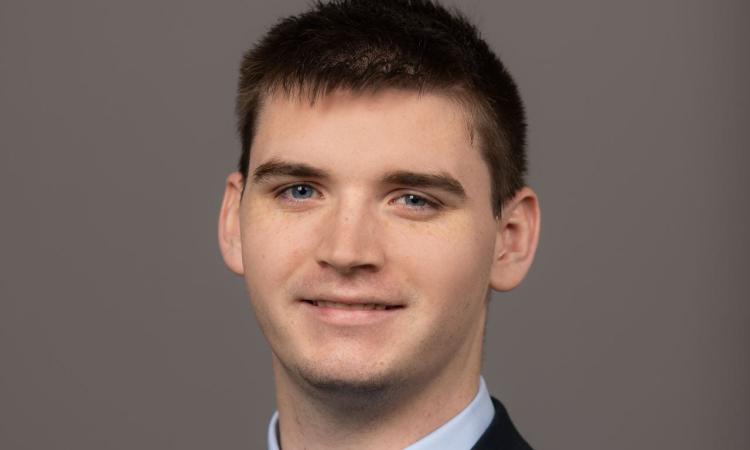
Aiden Wilson
Wilson was the math guy and took care of the data reduction and creating raw strain data maps from the DIC camera. The Louisville, Kentucky native hopes to enter the field as a GNC engineer.
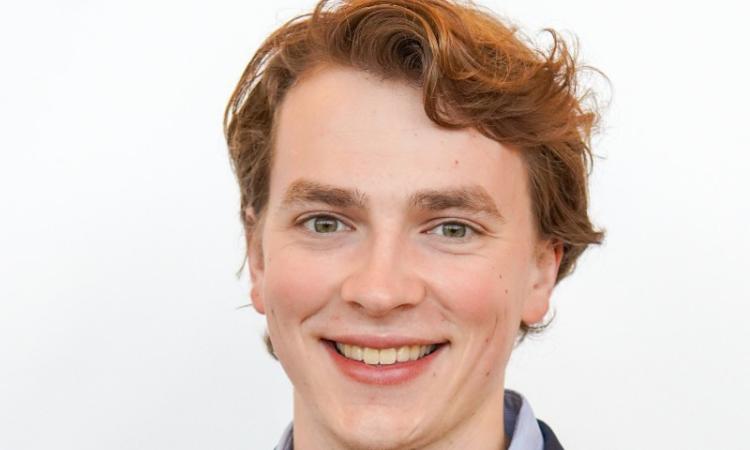
Ben Zabriskie
Zabriskie, who comes from Green Bay, Wisconsin, managed the manufacturing aspects of the project. His interests lie in data science and analytics, and he plans to go into finance after he graduates.
Ring the Bell
Third-year students Ethan Das and Cole Ajluni beat out 18 other teams with their project, Bell-Shaped Lift Distribution and Yaw Stability. Das covered the theoretical background work and Ajluni the fabrication, while both did experimentation.
The team of two decided to test the Prandtl-D wing to investigate its alternative lift distribution and the consequences of using it, such as the Yaw stability (left and right movement) and the aileron deflection (left and right movement from rolling motion). It seemed like a perfect challenge because this style of wing design isn’t often tested or fully understood.
The first stage was designing the wing. They used a NASA analysis design project model that looked into the bell-shaped lift distribution of the wing but had to redesign it from scratch to accommodate a smaller scale. Designing wasn’t easy using modern aerospace software because most aren’t created with the bell-shaped lift distributions in mind.
They 3D printed the 20-inch prototype. “We went with resin printing, broke it into three parts, and then epoxied it together at the Invention Studio,” Ajluni explained.
Manufacturing the Prandtl-D wing proved challenging because they used resin, which required more sophisticated printers. Once built, they took the prototype to the Georgia Tech Low Turbulence Wind Tunnel for testing.
“We had static Yaw stability, but we didn’t find a proverse yawing moment with aileron deflection because the actual structure of our wing wasn’t stiff enough, resulting in flexing of the wingtips to positive angles of attack,” Das explained.
Das and Ajluni are no strangers to competition and working in teams, as Das was a member of the student organization Design, Build, Fly (DBF) and Ajluni, the Georgia Tech Experimental Rocketry (GTXR) student organization.
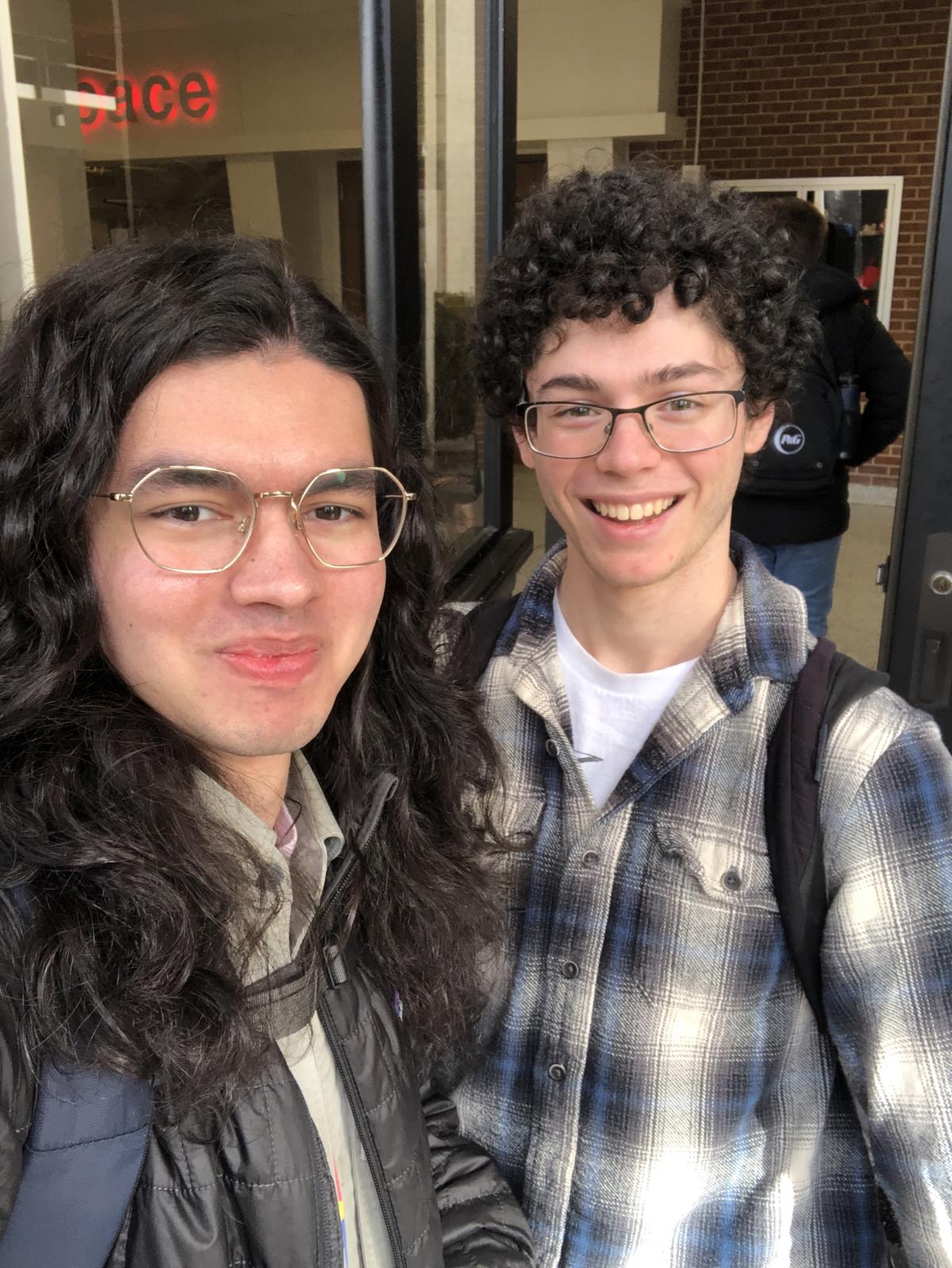
Robert Ajluni and Ethan Das
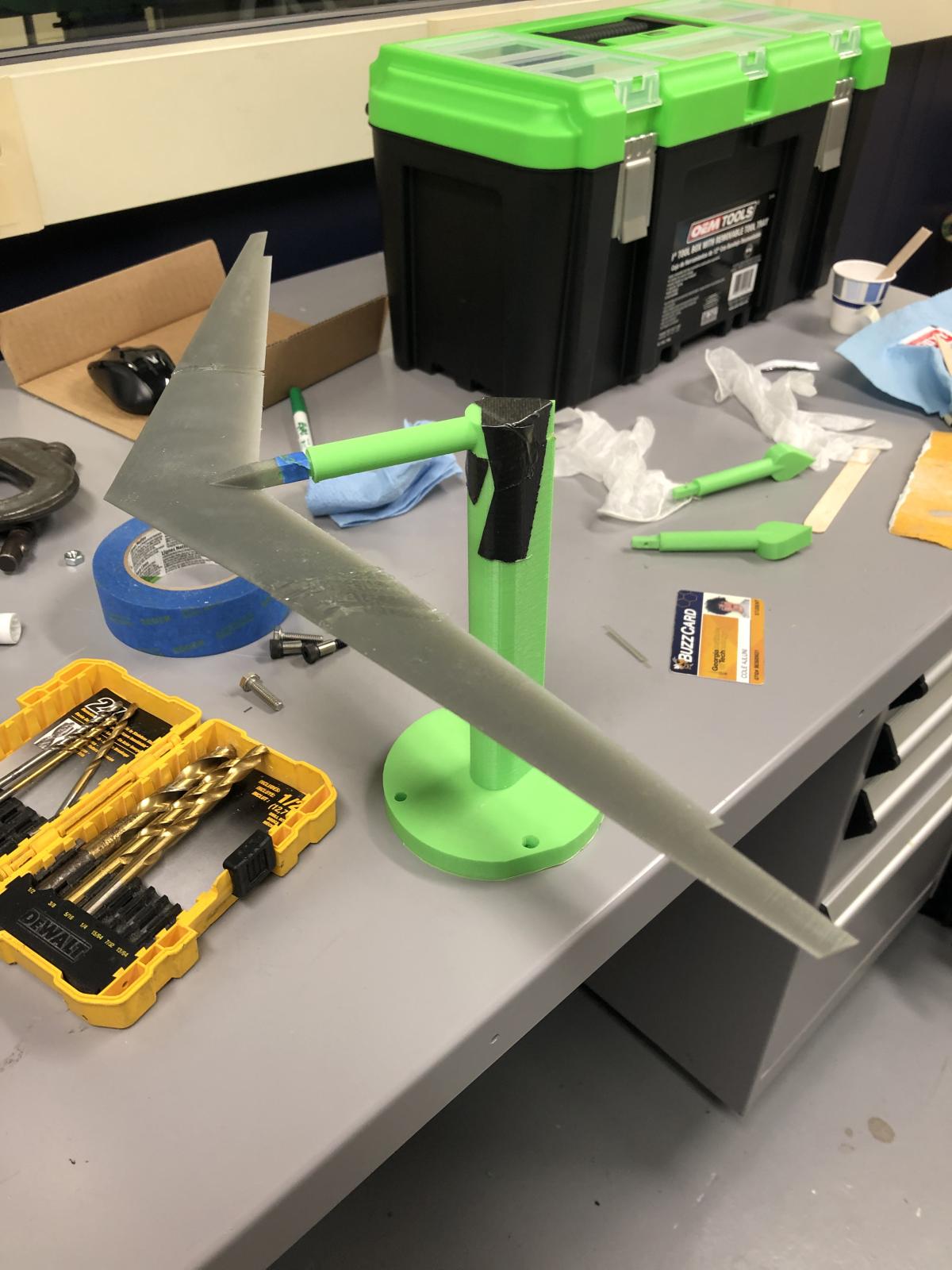
D-Wing Prototype
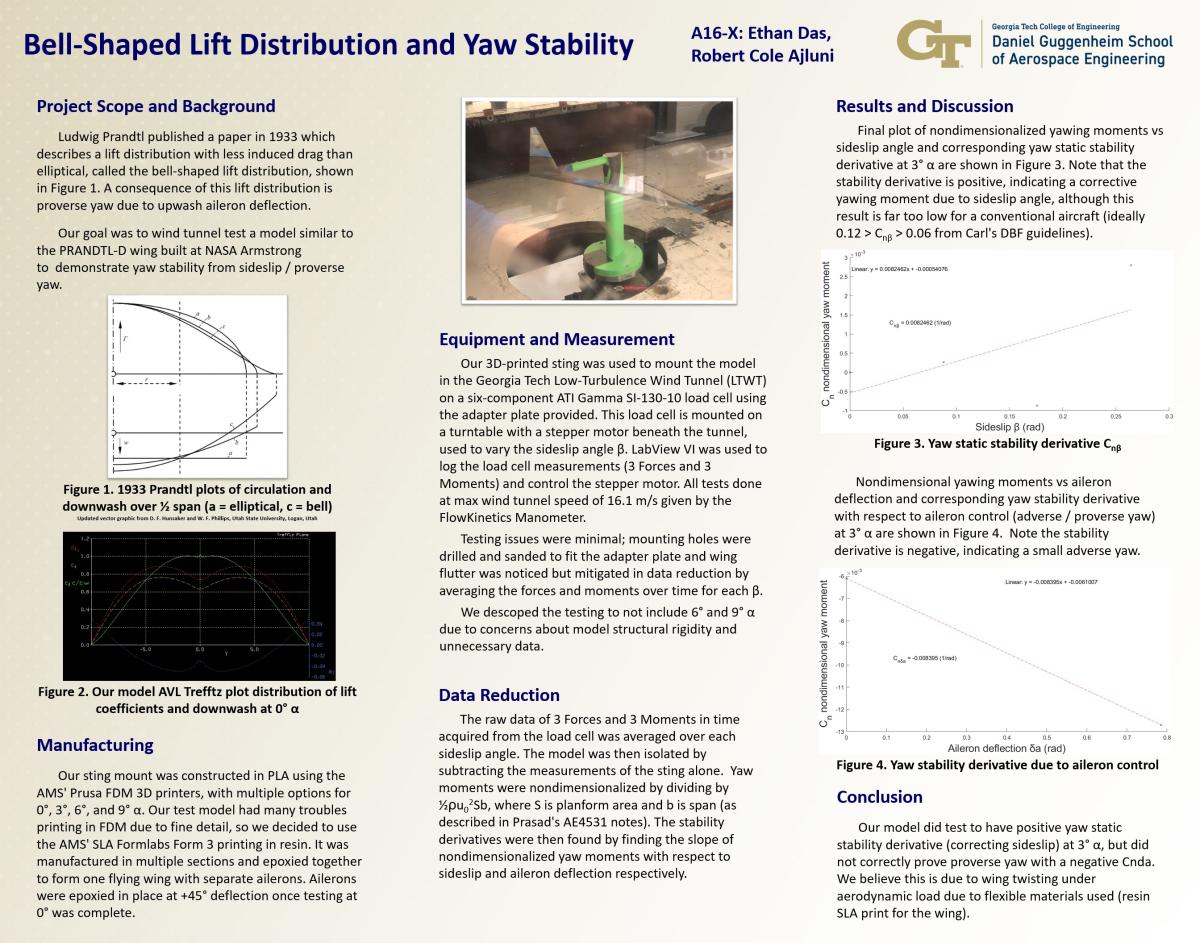
Bell-Shaped Lift Distribution and Yaw Stability Poster
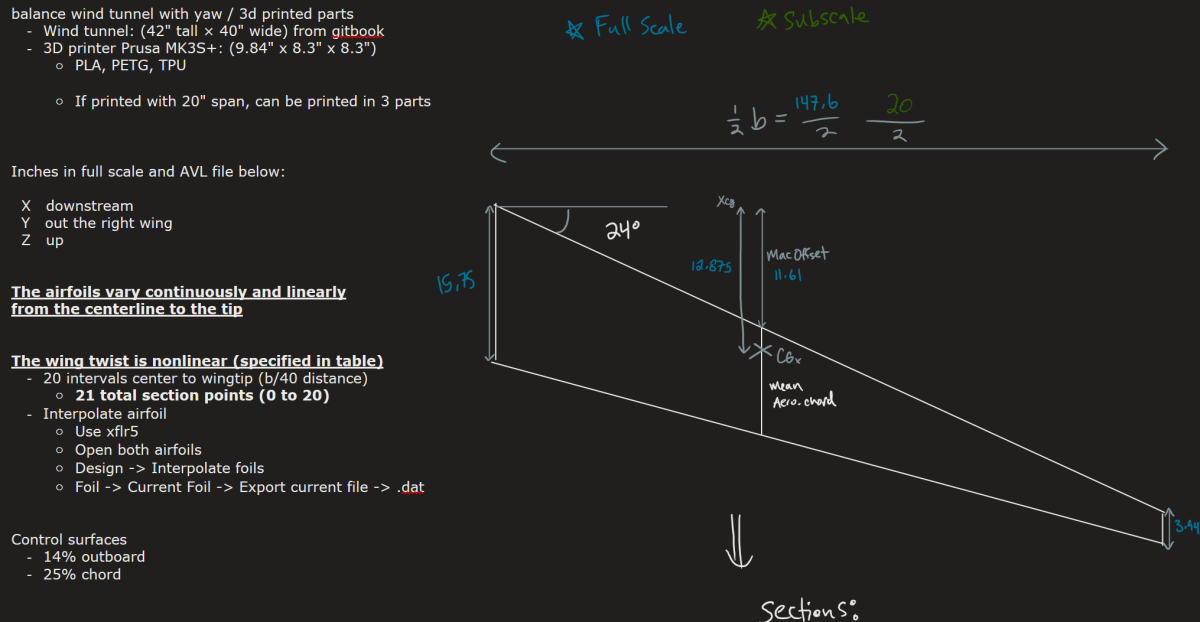
Athena Vortex Lattice Cnda
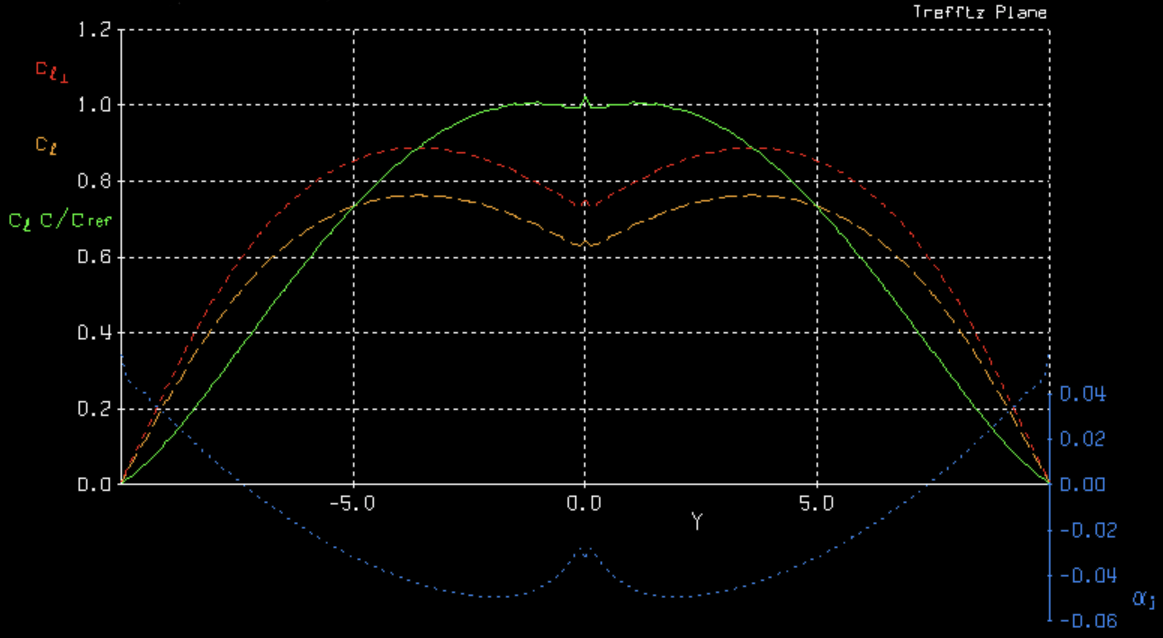
Lift distribution photo Resin SLS printing on Formlabs 3 in Invention Studio